The idea to design a print in place hinge is one I had in college. I wanted to create a protective case for an external hard drive that also has the mounting holes for my Raspberry Pi 3+. Figuring out the mounting holes for the PI was simple. The dimensions are clearly posted online so I first made a simple support piece with holes and space for zip-ties to hold the PI in place.
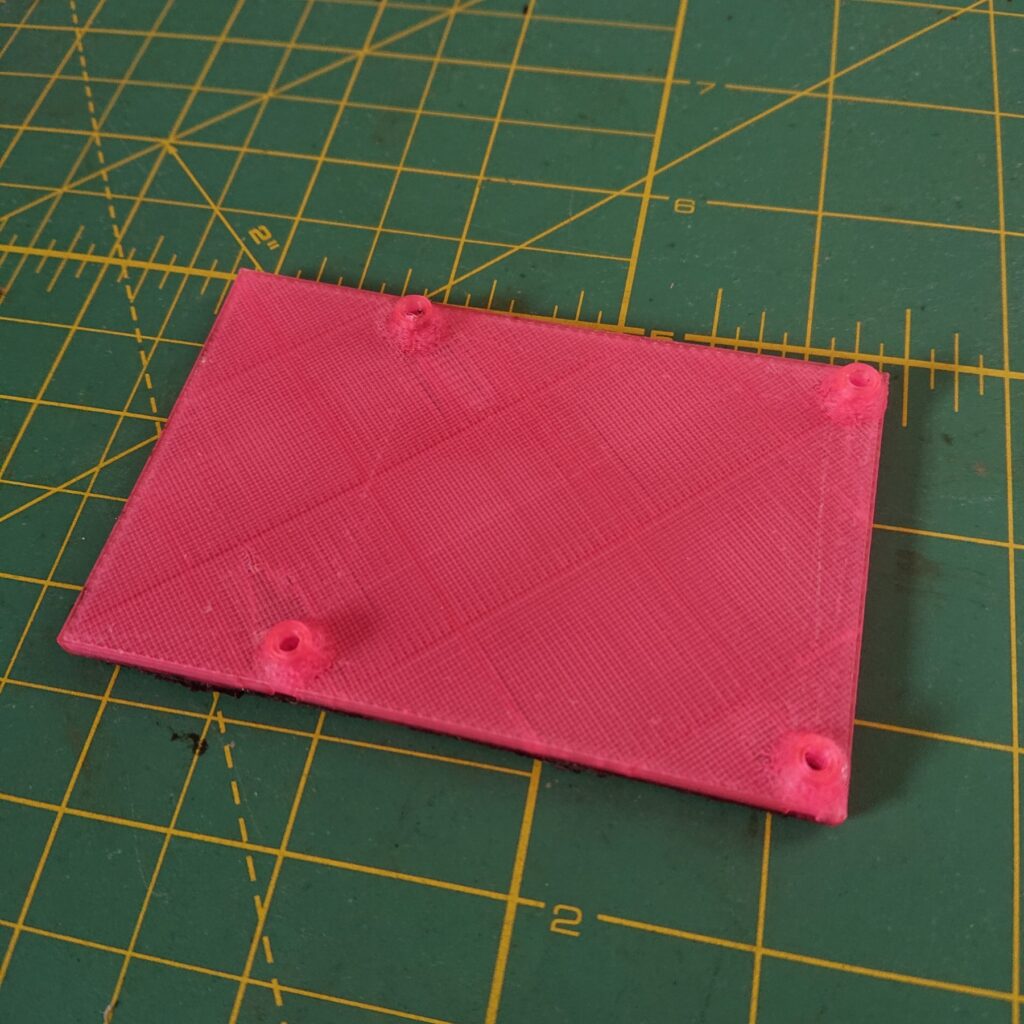
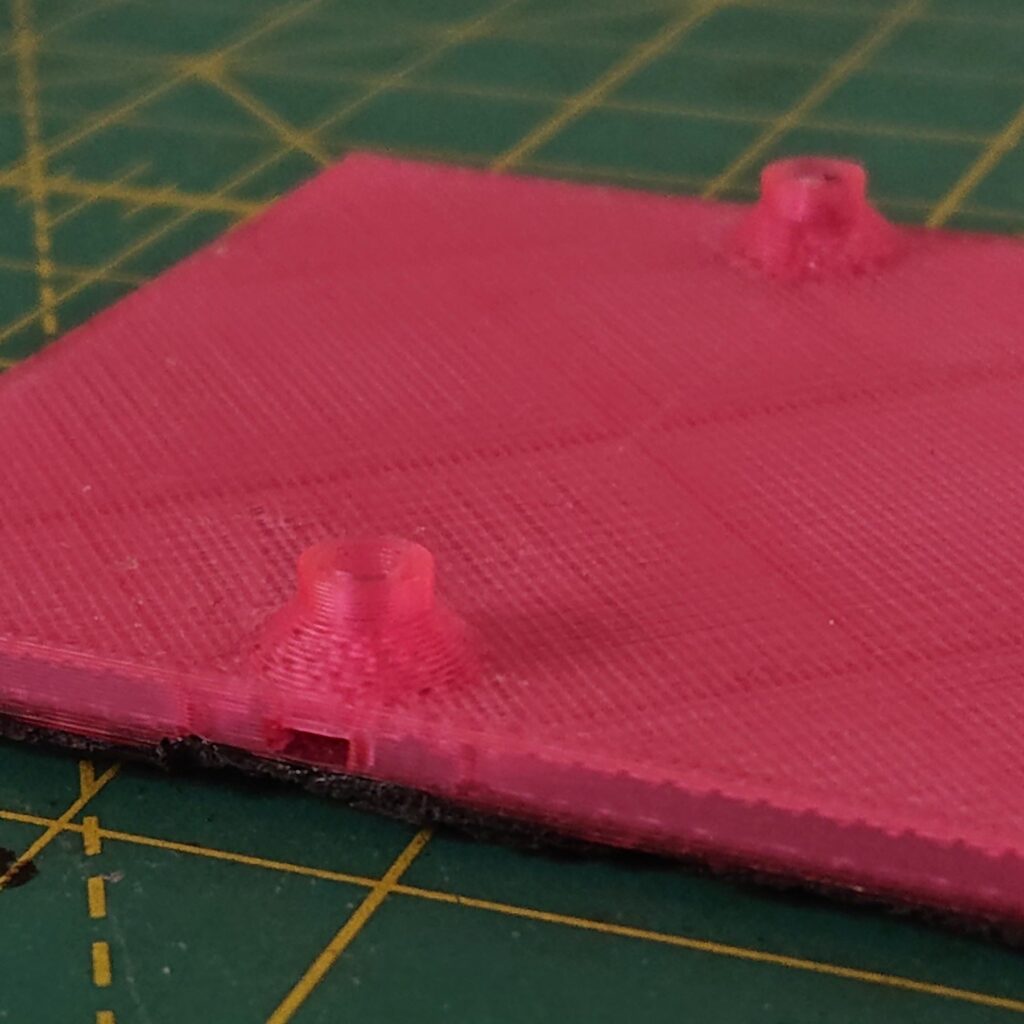
The intention was to use the PI and drive combo as a portable media center where a library of tv shows and movies can be easily hooked up with simply a power outlet and an HDMI cord. Since the initial idea was had, I have built and maintained a 12TB NAS storage server which hosts a Plex server with so much more media than I ever could have fit onto a single drive. With just an internet connection, any smart device can access the full library; clearly a better solution.
My first attempt at a P-I-P hinge was at the same time as an interest in printing basic geometric shapes. It was a simple container made of two halves of an isosohedron with a single hinge segment connecting the two. Interestingly, the filament ran out half way through the print so it happens to be two toned.
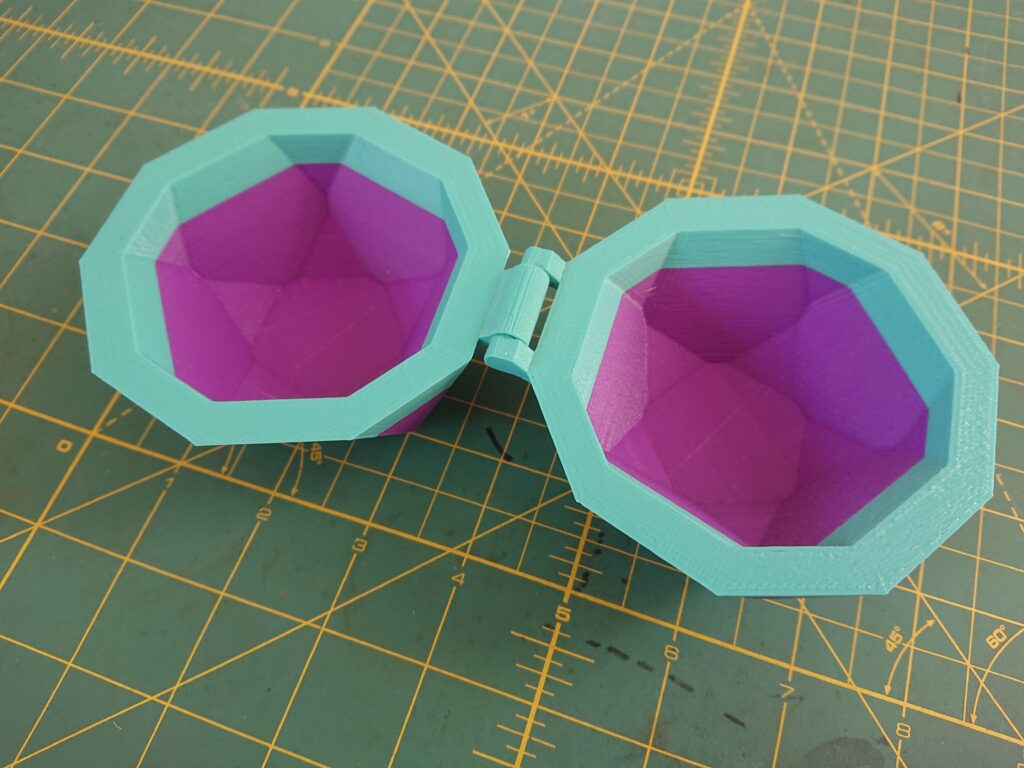
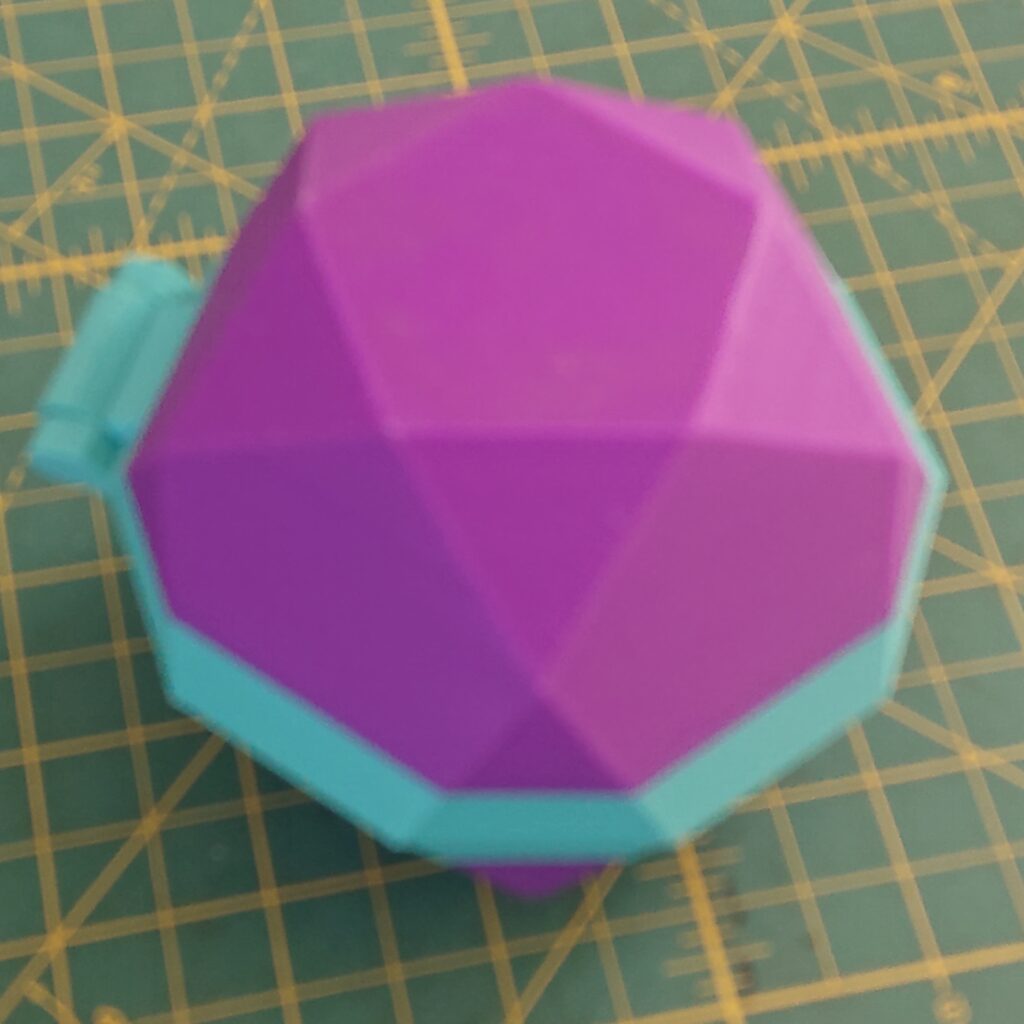
Shockingly, my first attempt at a P-I-P hinge was successful! I forget the specific tolerances of the hinge mechanism, but I do know it ended up pretty loose. I think I used around 1/16″ of tolerances all around (see below for more information on tolerances). It also doesn’t help at all that there was only one hinge section. With future designs I made sure to use multiple hinge segments.
I wanted the part to be special in that it could only be created using 3D printing. The pin of the hinge has a curve in profile view, making the pin narrower at the middle and wider near the ends. The outer part of the hinge used the matching curve, with some tolerance.
image of profile view wireframe of hinge
I figured that the pin of the hinge doesn’t technically need to be a cylinder, and that perhaps having the pin wider at the base and narrower down the middle would be better for supporting the thin plastic. Traditional manufacturing methods would not permit an axle being built like this as it would be practically impossible to assemble.
Future designs of P-I-P hinges don’t include this kind of complexity, though I did produce a working prototype of an external hard drive case that does. It uses four hinge units along the long side of the case. The bottom section only holds the drive with a hole for a USB connection. The top is trickier, with some raised sections designed to hold the PI support piece (seen above) and more space designed to hold SD cards or other devices.
image of ehd case
As mentioned, the hinge geometry is like the isosohedron design I used. The pins narrow near the middle. With four hinge sections, the action of the hinge actually is quite satisfying.
image of open hinge, hinge details
This was the longest print I had done to date. I had to leave it overnight at school, but I’m not sure the actual print time on it. When I noticed the layer shift in the print the next morning I was worried it would affect the hinge. To my surprise the hinge still worked. Unfortunately, the box no longer closed properly. The layer shift effect was doubled thanks to the design.
image of layer shift profile
A few years have passed since that point. I have left the convienence of college 3D printers and now am constantly looking for projects to do on my AnkerMake M5 printer. With that I needed software other than the free college accounts I had been using at that point. Near the end of 2022 I purchased a persistant liscence to Rhino 3D. Rhino includes many helpful features, one of which is the visual programming language known as Grasshopper 3D.
Image showing Rhino and Grasshopper
Below is my program to produce custom sized P-I-P hinges. There are special settings to specify the overall tolerance amount, number of hinge segments, and more.
Scalable image of hinge program
This hinge generator has produced things such as this prototype printed barbell collar.
image of barbell coller(link when clicked)
As well as smaller hinges to push the tolerances.
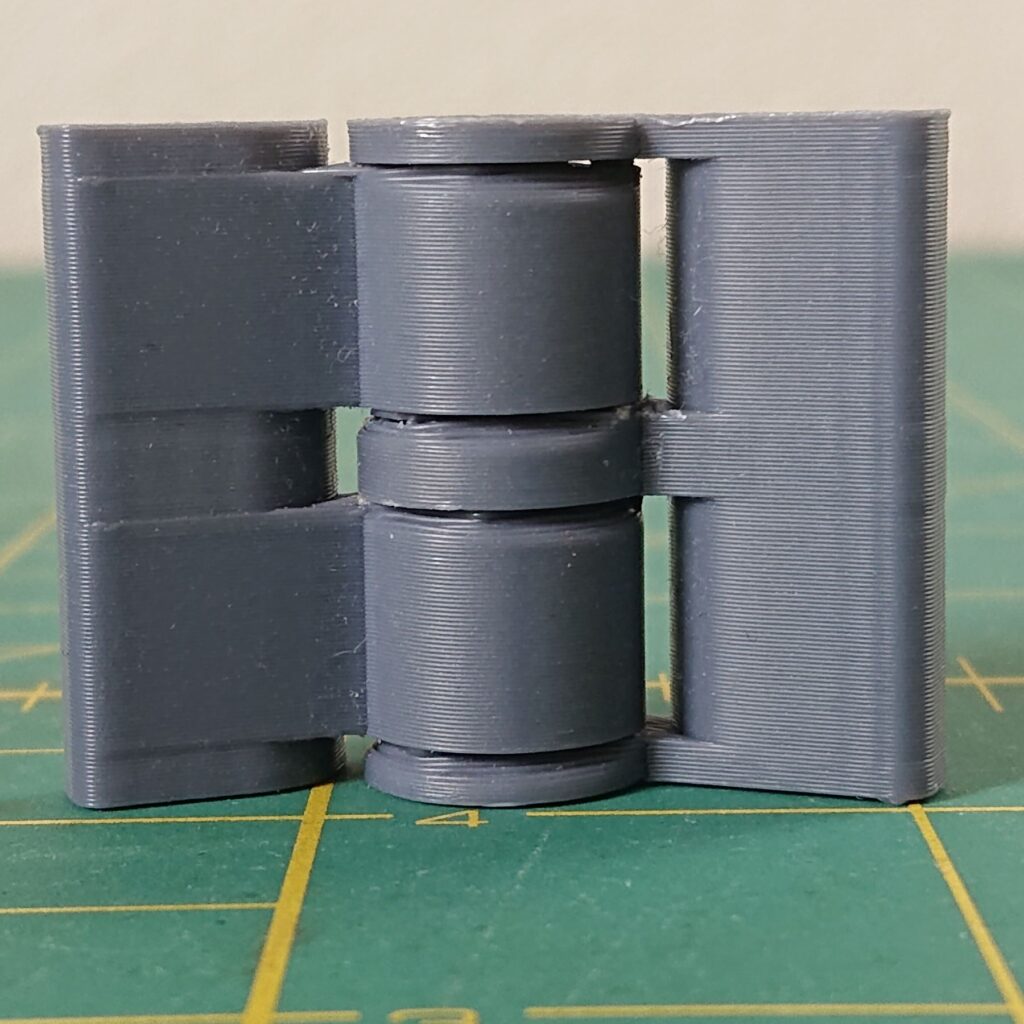
I find that 0.4mm of tolerance between all surfaces is plenty good enough for standard applications. I initially tried this as it is the nozzle diameter of the printer I use, as well as most of the printers I used at school. 0.4mm seems to me to be the standard residental printer resolution. With a more precise printer, and maybe some layer settings, slicing tolerance for example, the tolerance might be able to be brought down. Naturally, lower tolerances should create tighter fitting hinges.
Leave a Reply